Welcome to The Gigacasting Newsletter
New here? Subscribe
Zeekr 9X Gigacasting, a Cornerstone of Safety Design
To safeguard third row passengers in rear end collisions, the Zeekr 9X employs Geely's third generation of one piece rear underbody Gigacastings.
This component reduces the number of parts by over 80, eliminates more than 1,000 welding points, significantly boosts body rigidity, and decreases deformation from rear impacts by 16%.
While the crash test speed wasn’t initially specified, Zeekr later confirmed the vehicle body can withstand a rear end collision test at 105 km/h.
Additionally, an aluminum die cast C and D pillar structure reinforces the upper body. Compared to traditional designs, this reduces the part count by 8, increases torsional stiffness by 12.5%, and cuts weight by over 5 kg.
In a 50 km/h side collision, the vehicle’s safety performance exceeds the Chinese national standards by more than 20%.
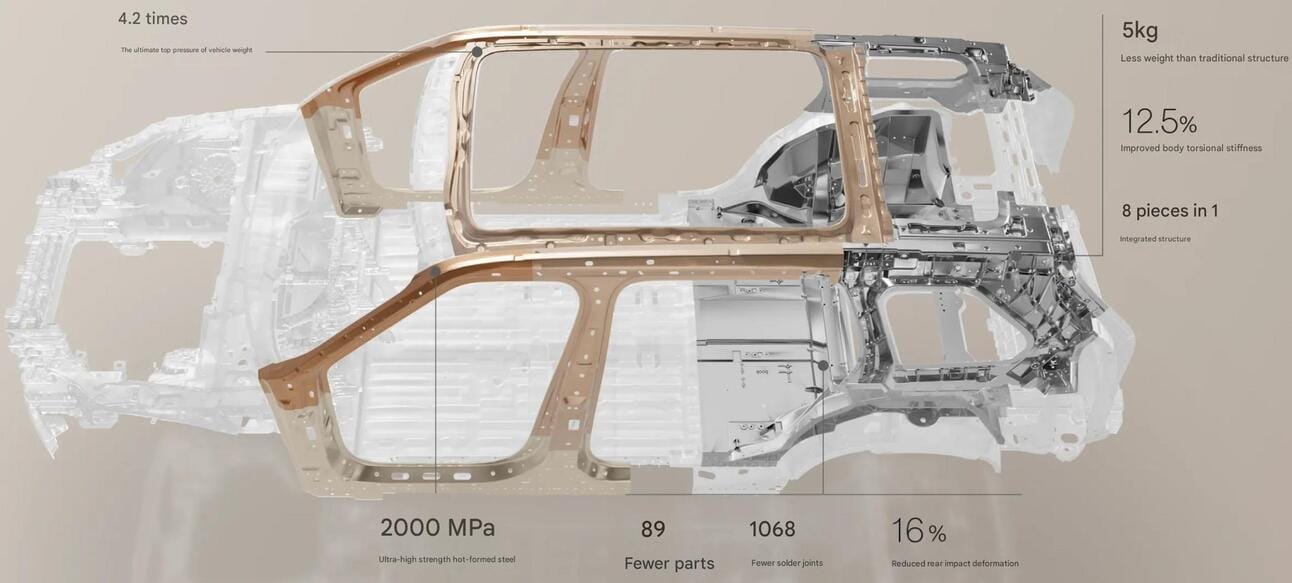
Judging by the image above, the RUB Gigacasting design features wide wheel arches and a large flat area beneath the second row passengers to maximize part integration, and therefore reducing more parts within the casting and thousands of processes on the factory floor.
This design prioritizes reducing part count over minimizing slight weight inefficiencies from incorporating large flat surfaces, such as the rear floor and wheel arches, directly into the casting.
Notably, the crash cans appear to be separate from the main casting. In a moderate speed rear collision, the integrated crash cans in a Tesla Model Y’s rear casting absorb impact and may deform, potentially complicating repairs.
However, Tesla’s “Gigacast Sectioning” method, outlined in my recent article, enables cost effective repairs for consumers.
In contrast, Zeekr employs separate crash cans, similar to traditional body in white (BIW) designs, facilitating simpler repairs.
Note: The RUB casting in the thumbnail differs from the one used in the new 9X model. HD images of the new Gigacasting are currently unavailable. The analysis is based on the biw images released by Zeekr
Magpro Launches Ingot Chipper to Supply Magnesium Alloy Chips For Thixomolding
Camden, TN – Magpro LLC officially commissioned a new ingot chipper at its Tennessee facility, enabling the immediate supply of magnesium alloy chips for thixomolding applications.
“Thixomolders can now purchase magnesium alloy in chip form direct from a domestic magnesium producer” said John Haack, President of Magpro, LLC.
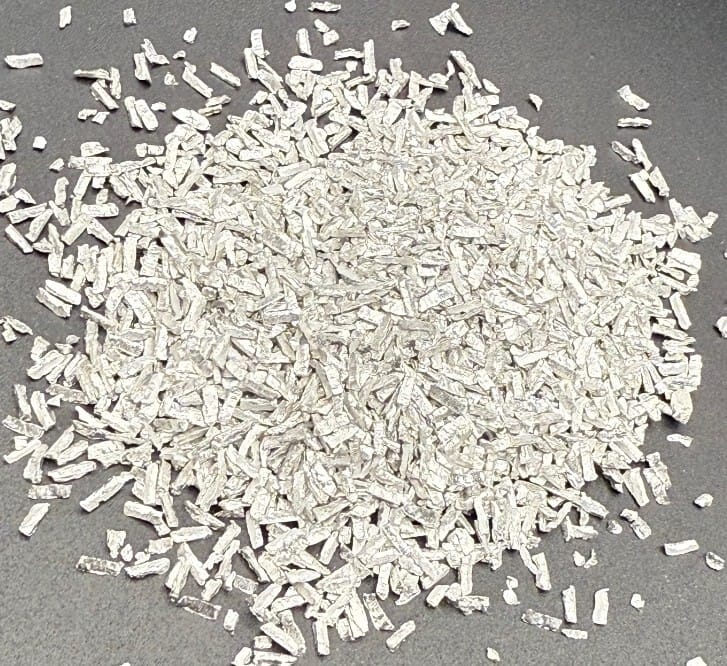
magnesium chips
American foundries can now purchase magnesium alloy in chips directly from a domestic producer, streamlining their supply chain. The company has been testing the new chips with select customers over the past few months, receiving positive feedback.
One customer highlighted the benefit, stating, “I now have a full service magnesium supplier that can toll 100% of my magnesium scrap back into magnesium chips.”
The ingot chipper project began in Q4 2024 with the construction of a new building at Magpro’s magnesium recycling facility. Production of the thixomolding chips kicked off in early 2025.
Due to strong demand, Magpro is already planning to expand capacity and are breaking ground on a new 7,500 square foot steel building to house two additional ingot chippers set to be commissioned in Q4 2025.
That’s not the end, if demand for this form of product keeps increasing, then more chippers will be installed.
About Magpro LLC
Founded in 2003, Magpro LLC specializes in recycling type 1 and non-type 1 magnesium alloy scrap for customers across North America.
The company produces pure magnesium and magnesium alloys in chip, ingot, and sow forms. Although their annual production capacity is not mentioned, Magpro told me they maintain a 20% surplus to demand.
In addition, Tom Kurilich from Magpro will speak at a webinar, hosted by the International Magnesium Association (IMA), titled; “Shaping the Future: New Frontiers in Mg Thixomolding”.
You can register here if you want to attend.
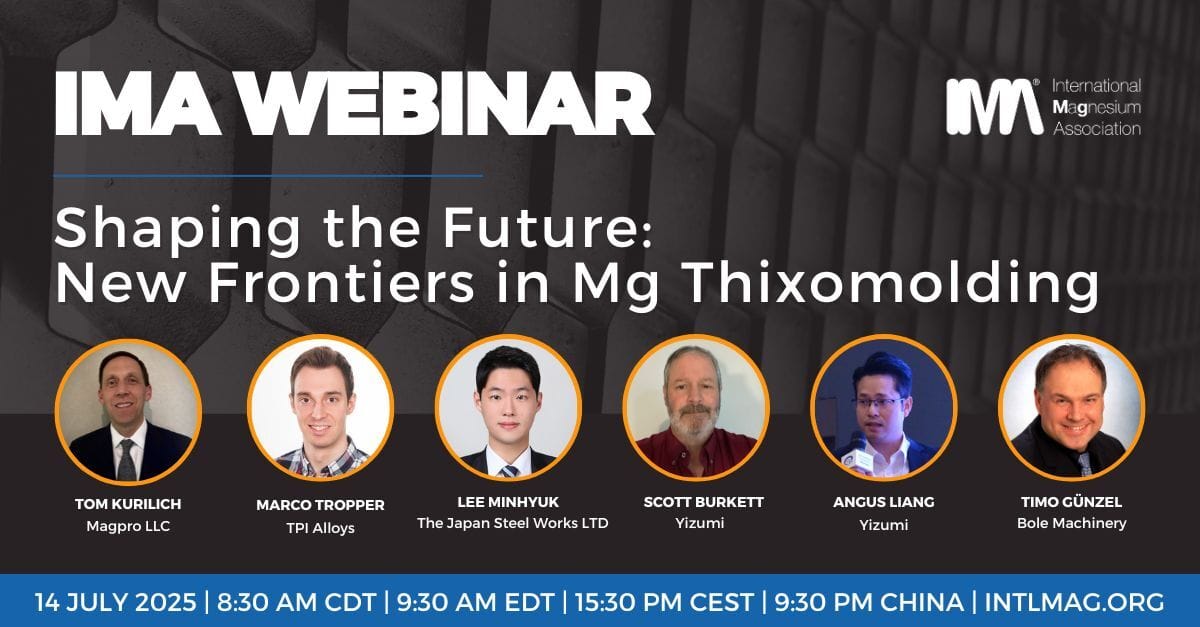
❌ Don’t leave your insights to chance with social media algorithms
✅ Subscribe for free to receive updates delivered to your inbox
💡 Join thousands of industry professionals who rely on The Gigacasting Newsletter for the latest updates on Gigacasting, Thixomolding, Rheocasting, and more
📨 I’m dedicated to keeping your inbox clutter-free with updates sent every one to two weeks
Nio Onvo L90 Adopts Gigacastings
Nio unveiled the Onvo L90, the flagship model of its sub brand Onvo, a fully electric vehicle prioritizing affordability and putting particular emphasis on its exceptional safety for third row passengers, particularly children.
Central to the L90’s body in white safety architecture, once again, is Nio’s advanced Gigacasting technology. “We’ve engineered the third row with enhanced safety features to provide best-in-class protection for every seat” said William Li, Nio’s CEO, during the unveiling.
The L90 incorporates a rear underbody (RUB) Gigacasting that forms the third row floor, eliminating 72 parts and reducing weight by 11.7 kg. This component uses Nio’s proprietary Nio 2 aluminum alloy, developed with partners and suppliers is comparable to the C611 EZCast.
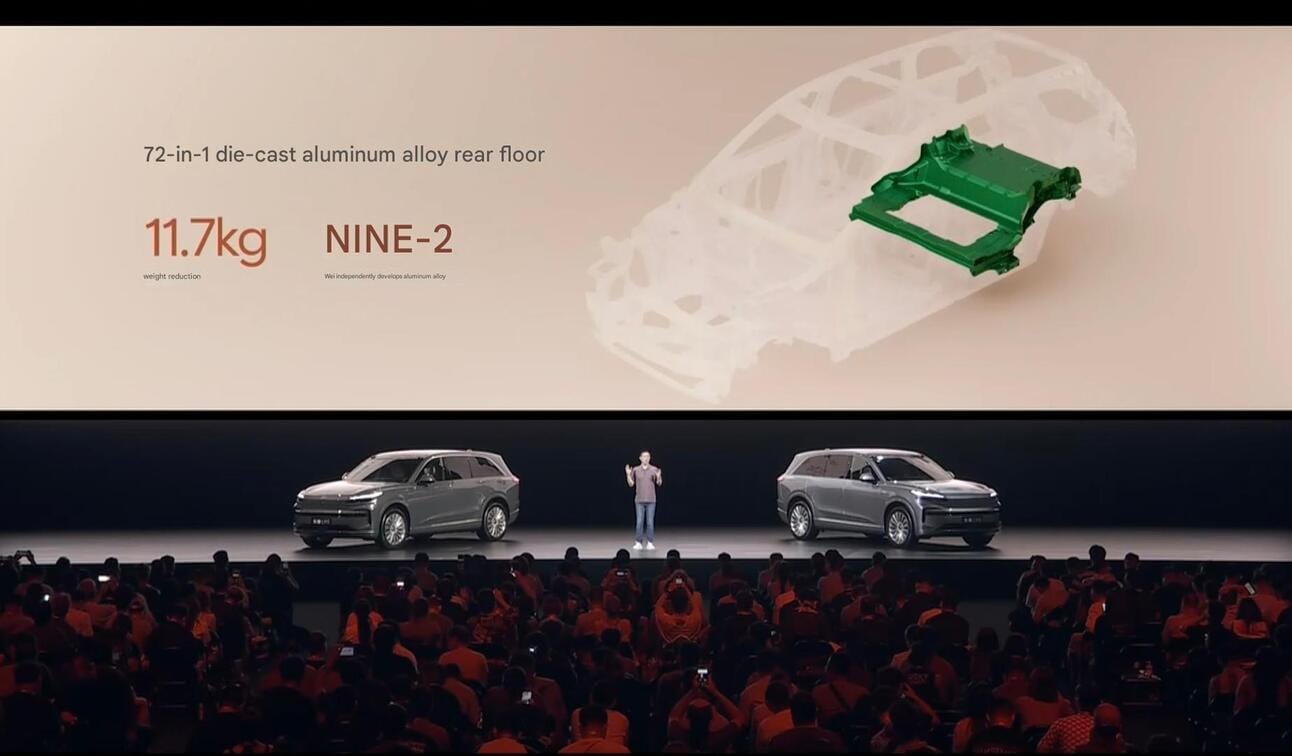
Unlike Tesla’s integrated designs, the L90’s rear underbody excludes crash cans, which are constructed separately using traditional methods. For a deeper analysis, see my review of the Zeekr 9X above.
In contrast to the Zeekr 9X, seen previously, the L90’s Gigacasting design omits wheel arches, aligning with other NIO models like the ES6, EC6 and ET9 to name a few.
This approach streamlines the casting process by optimizing molten metal flow, improving part cooling, reducing weight, and minimizing storage and shipping space requirements.
However, this design necessitates a separate process to attach wheel arches, slightly reducing efficiency in part count, body in white shop size optimization, and overall cost savings.
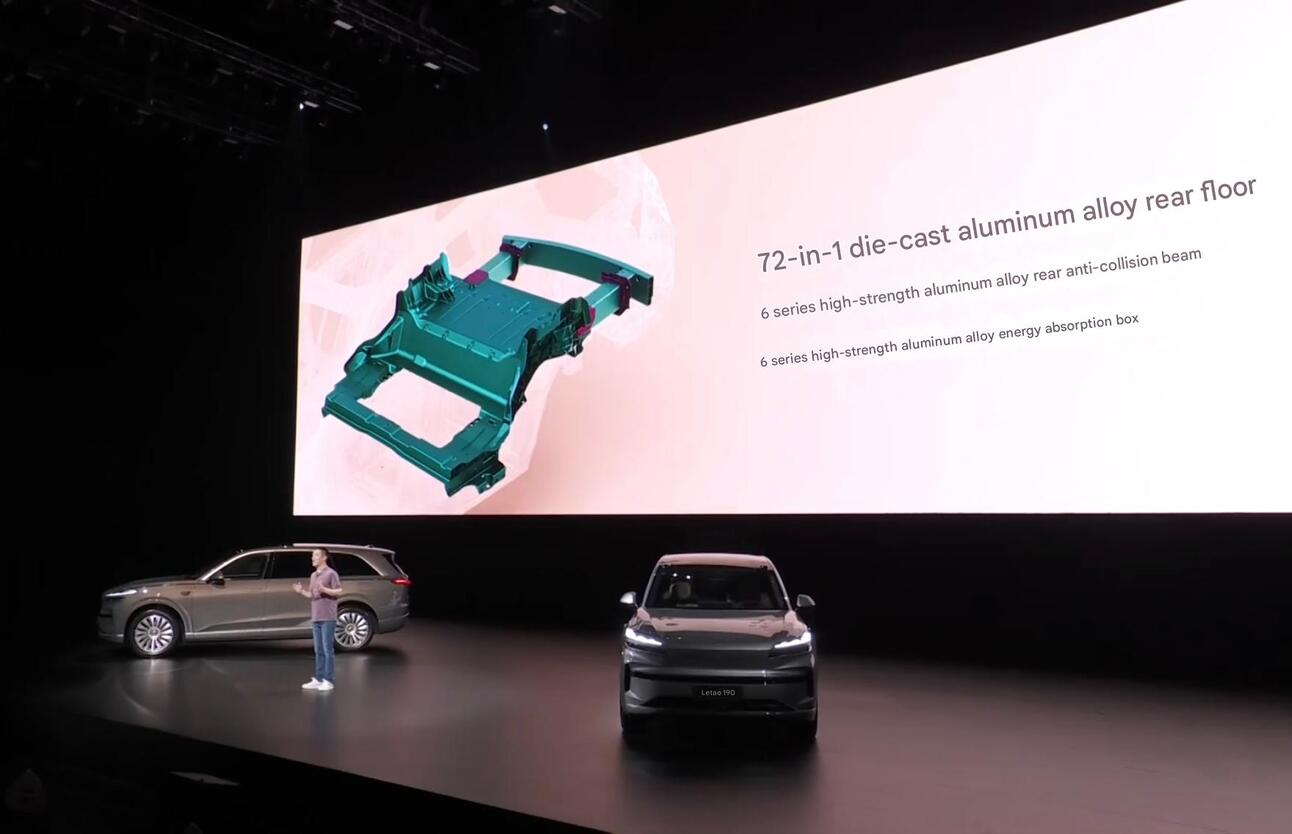
Dongguan Eontec’s 3000T Magnesium Alloy Thixomolding Machine To Begin Production
The JSW 3,000 ton magnesium alloy semi solid injection molding machine at Dongguan Eontec, Ltd has been installed and is undergoing final testing. It is slated to enter full production within a week.
Supplied by Japan Steel Works (JSW), the machine will manufacture automotive dual and triple car displays as well as Cross Car Beam brackets (CCB), offering significant advantages in precision, lightweight and efficiency.
Unlike traditional methods, thixomolding eliminates the need for a melting furnace or protective gas, as the molten metal remains isolated from environmental oxygen throughout the process.
Dongguan Eontec has integrated multiple JSW semi solid thixomolding machines, installing several production lines with machines with clamping forces ranging from 280 to 3,000 tons.
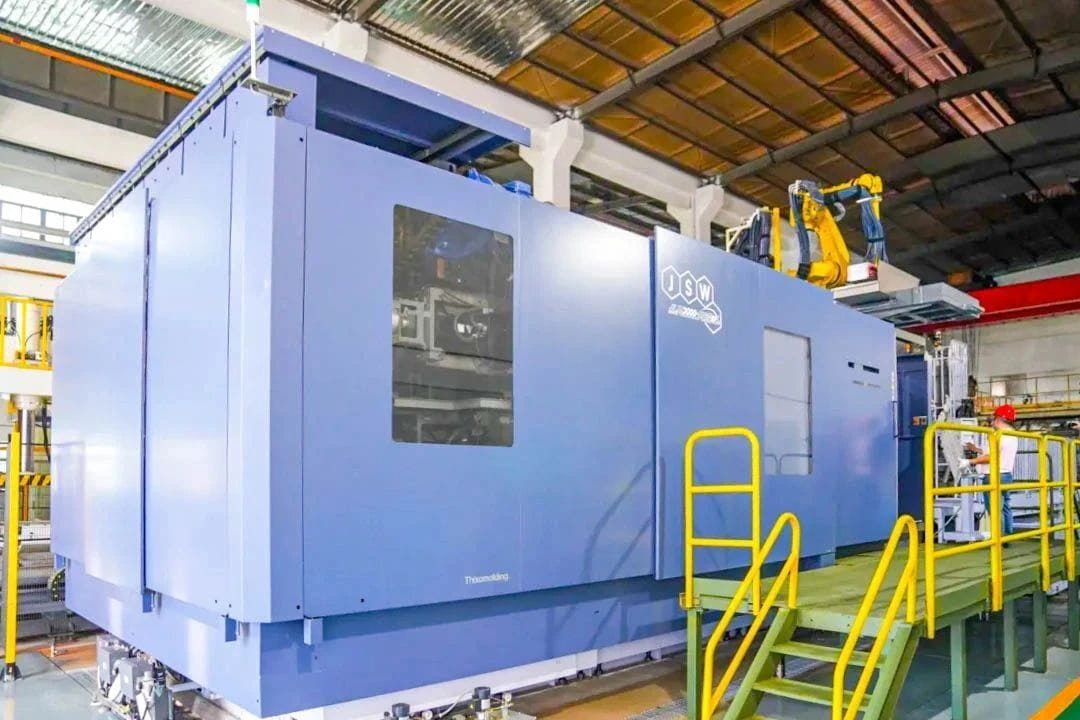
🎯 Reach the heart of the die casting industry with The Gigacasting Newsletter, the world’s most targeted newsletter and website for die casting professionals.
🌐 With thousands of engaged subscribers and high-impact ad placements, your business can connect directly with decision-makers and innovators in the field.
📩 Reply to this email to discover how The Gigacasting Newsletter can elevate your brand. Secure your spot today!
Last Article: