Welcome to The Gigacasting Newsletter
New here? Subscribe
Now Official, Toyota's Shanghai Factory Will Use Gigacastings
In February 2025, Toyota announced that Lexus would establish a fully owned production facility in Shanghai dedicated to pure electric vehicles, with an initial annual capacity of 100,000 units and production slated to begin in 2027.
I initially reported that this facility would likely adopt Gigacasting technology and produce the Lexus LF-ZC, set for a 2026 launch and initial production in Japan. Recent details from the factory permits confirmed this information.
This will be China's first wholly owned automotive plant by a foreign company, for both domestic and international sales, after Tesla established Giga Shanghai in 2019.
The facility will manufacture the new Lexus model using Toyota’s cutting edge technologies, including Gigacasting, self propelled production lines, and an unboxed assembly process to reduce factory investment and accelerate mass production setup.
Recent exclusive information indicates that Toyota is close to signing a deal for 9,000 ton die casting machines for the Lexus plant in Shanghai, with Haitian as the likely supplier.
In addition to serving the Chinese market, 20% of the plant’s output will be exported to Europe and Southeast Asia.
Spanning 615,700 square meters, the plant’s development is divided into three phases:
• Stamping, die casting, body-in-white, painting, general assembly, and battery pack assembly.
• A dedicated battery workshop and an office building.
• Expansion of stamping and die casting, plus an additional battery workshop.
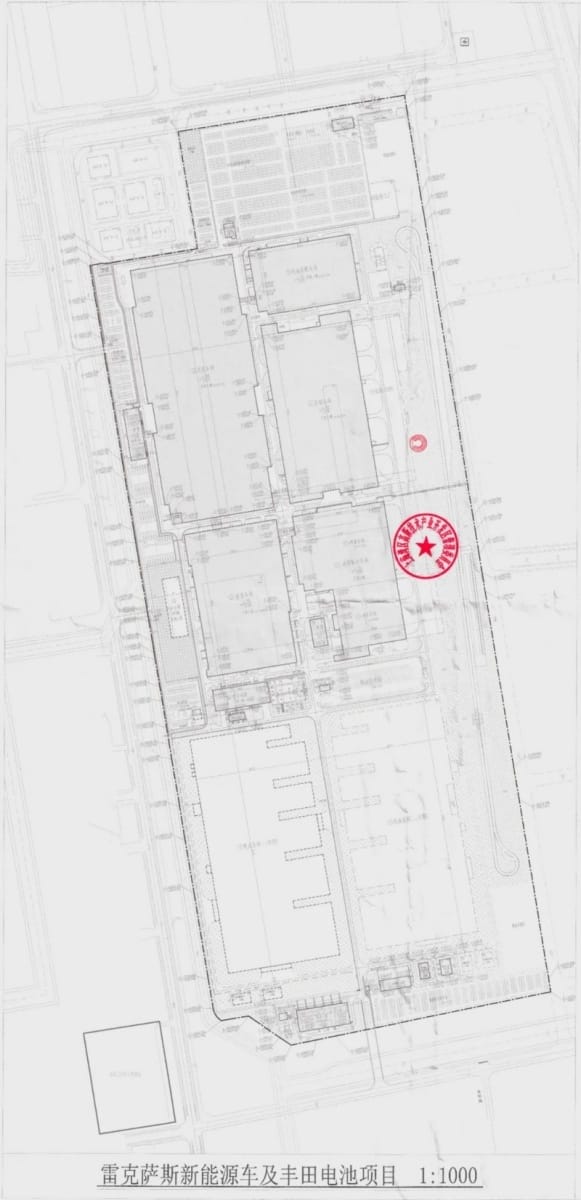
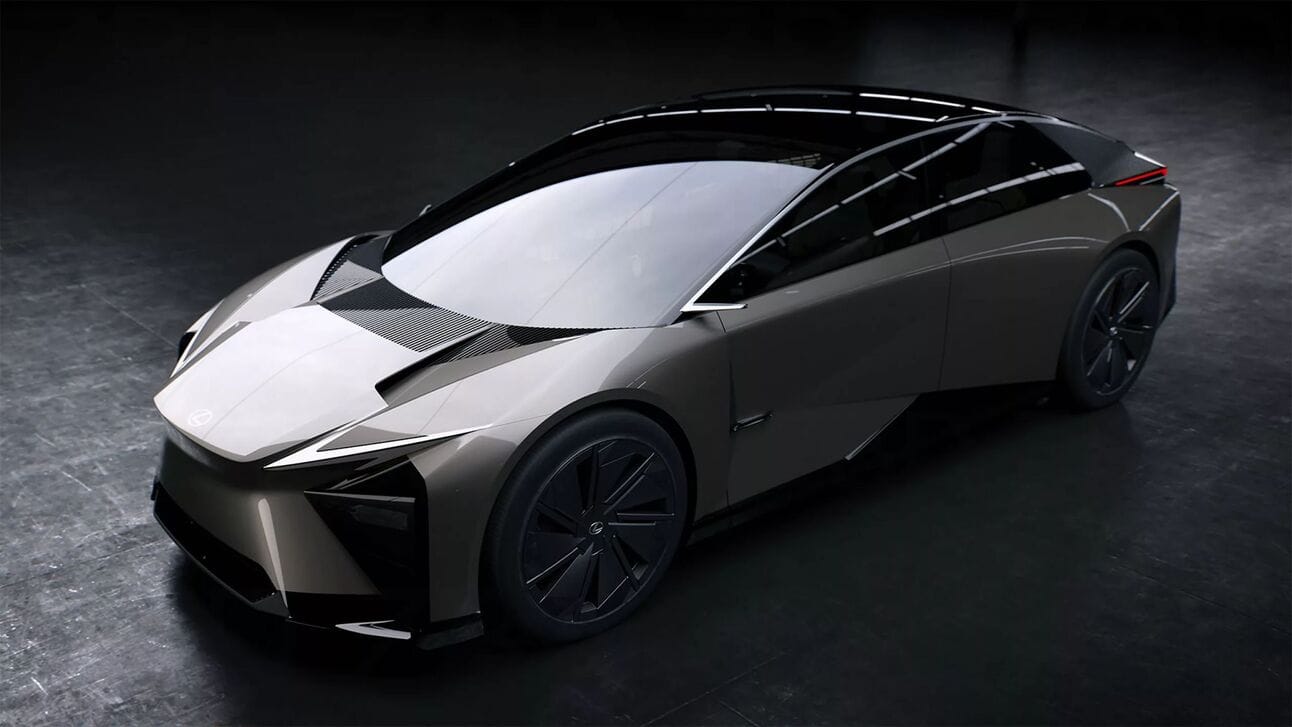
Lexus LF-ZC
Magrathea Launched Its Magnesium Chloride Electrolyzer
Magrathea, a company based in California developing a new generation of electrolytic process for making carbon neutral metal from seawater and brines, has launched its magnesium chloride electrolyzer, a machine that uses electricity to split magnesium salts to make magnesium metal.
Here is how it works, based on information released by the company.
Seawater, salt lakes, and groundwater contain small amounts of magnesium (about 0.1% by weight in seawater). By purifying and drying this brine, solid magnesium chloride salt is obtained.
Magrathea, initially sourcing this salt from Cargill, feeds it into an electrolyzer heated to 700°C (1,300°F) and runs electricity through the molten salt to split the magnesium from the chlorine, forming magnesium metal.
Standard electrolyzers need constant electricity to keep salt molten, with precise temperatures to avoid solidification, which can disrupt the process or damage equipment.
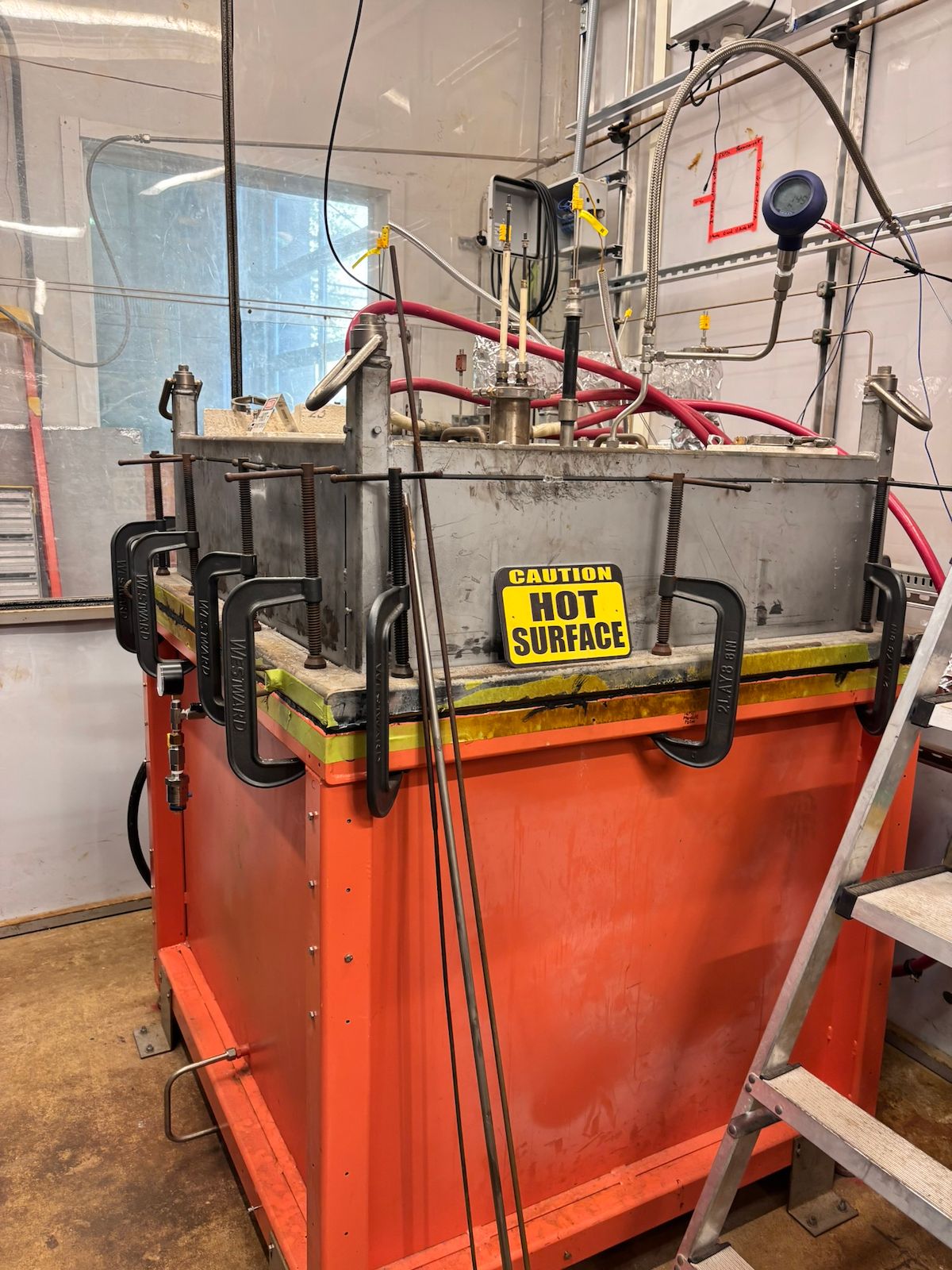
Magrathea’s next generation magnesium chloride electrolyzer.
Magrathea’s innovation runs the electrolyzer 100°C hotter than required, using excess heat to dry incoming magnesium salt.
This allows intermittent operation, running during cheaper electricity prices or when renewable electricity is available, lowering costs and emissions.
Magrathea’s California pilot plant produces 1,814 kg (4,000 pounds) of magnesium annually. The company plans to deploy its technology at a scaled facility by 2027 to produce up to 900 tons (2 million pounds) of magnesium per year.
After that… 📈
Magnesium is one of the most important critical materials, but NATO countries face a dire shortage of non-China supply.
Western nations must view this supply crisis as a national security emergency.
First 20 Inch Magnesium Rims In Series Production
Dongfeng Motor has launched the world’s first 20-inch magnesium thixomolded automobile wheel in series production.
Crafted from a stainless magnesium alloy, the wheel is manufactured using a 3,000 ton magnesium semi-solid injection molding machine, known as a “Thixomolding” machine.
This magnesium alloy wheel is 30% lighter than a comparable aluminum alloy wheel, significantly reducing rolling resistance. Dongfeng reports a 20-fold improvement in damping performance.
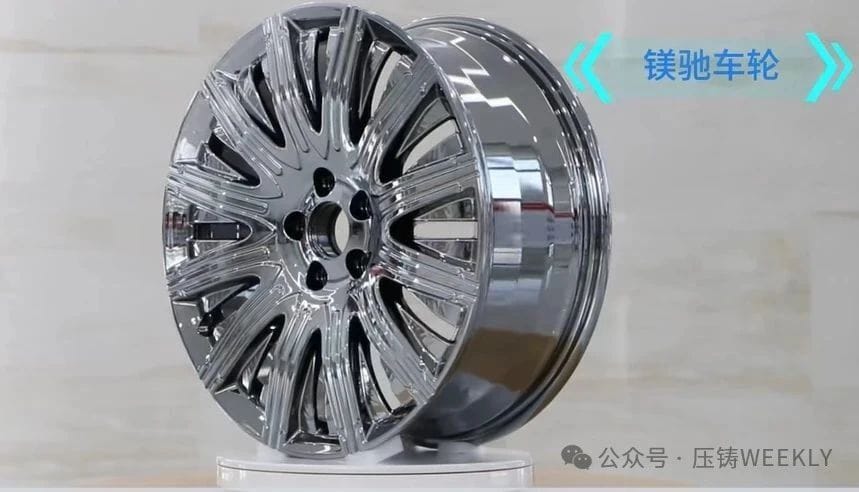
In April, I covered Bole Machinery’s announcement of the successful trial production of this innovative wheel;
Leveraging semi solid injection molding technology, the research team utilized a high strength, corrosion resistant magnesium alloy developed by Shanghai Jiao Tong University along with the MTX3000D two platen thixomolding machine developed by Bole Intelligent Technology.
Bole’s CTO, Timo Günzel celebrated the achievement on LinkedIn and said that these are set to be “the first 20 inch rims made of magnesium using the thixomolding process, which will go into series production in the automotive industry in China”.
With a shot weight of over 16 kilograms, this achievement not only marks a significant step in wheel production but also sets a new world record for the largest injection volume of thixomolded magnesium alloy parts.
Dongfeng Motor's Gigacasting Project To Start Mass Production In June 2026
Dongfeng Motor is actively aligning with China's national strategy for electric vehicles by advancing its integrated Gigacasting technology.
The company announced their dedicated Gigacasting plant is on track to begin mass production in June 2026, featuring the world’s largest die casting machines with 16,000 and 10,000 tons of clamping force.
Manufactured by LK Machinery, these machines are expected to produce 200,000 lightweight components annually.
As of the last updated in March 2025, local Wuhan media reported that the steel structure hoisting of the main building was over 90% complete and a 16,000t die casting machine was being installed.
About Dongfeng’s Gigacasting plant;
The project focuses on developing, manufacturing, and selling ultra large Gigacasting structural components for new energy vehicles, such as rear underbodies and battery trays.
Backed by a 226 million yuan investment ($31.2 million at the time of announcement), construction began in April 2024. Upon completion, the plant will house six die casting production lines, commissioned in three phases.
Tesla Quick Update
Tesla received additional equipment related to the new furnaces which support on-site recycling of scrap from Gigacasting operations, as well as recycling aluminum from external sources. Read more about this project here.
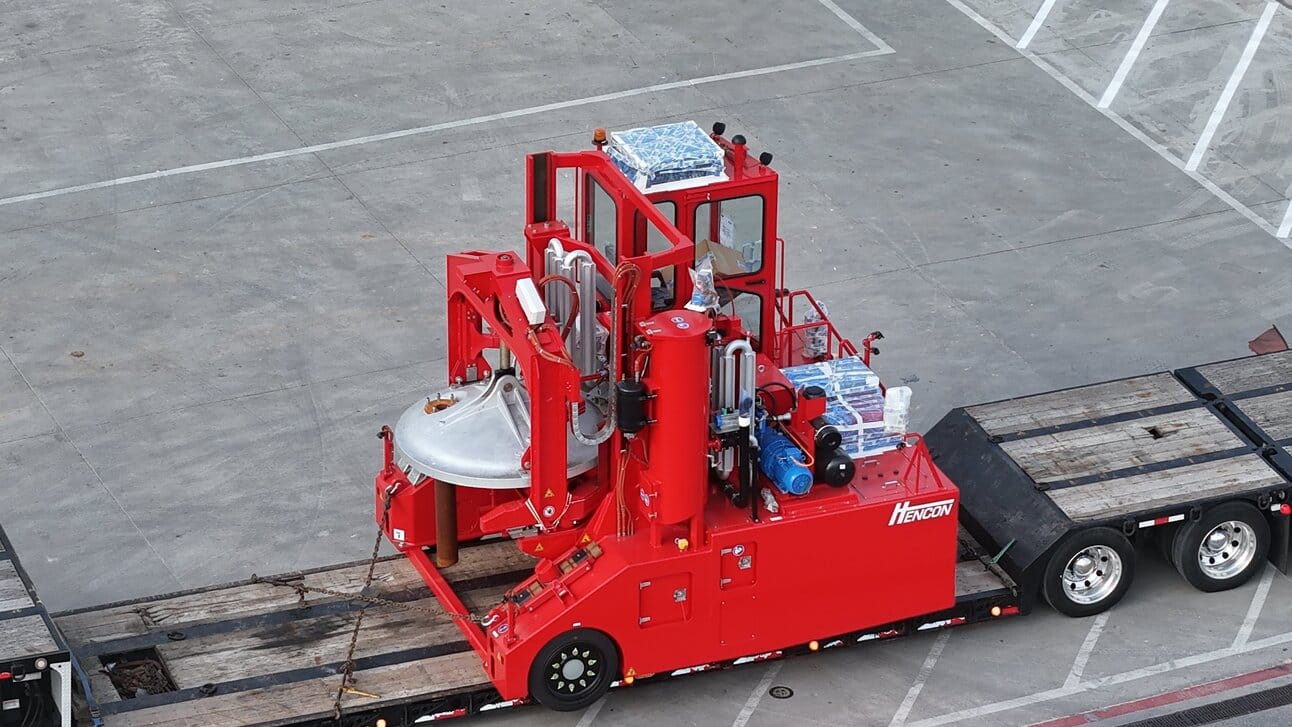
Hencon Aluminum transort vejicle. Source: https://x.com/JoeTegtmeyer/status/1931003221163556949
At Gigafactory Texas, the Tesla team placed a Cybertruck front underbody (FUB) Gigacasting alongside a Cybercab FUB Gigacasting in the logistics lot.
Thanks to drone pilot Joe Tegtmeyer flying over the site and recording video footage, we can see that the difference in size between the two is quite substantial.
Over 500 Cybercab front underbody castings have already been produced and spotted on site. Read more about Tesla’s dedicated Robotaxi platform and its Gigacastings here.
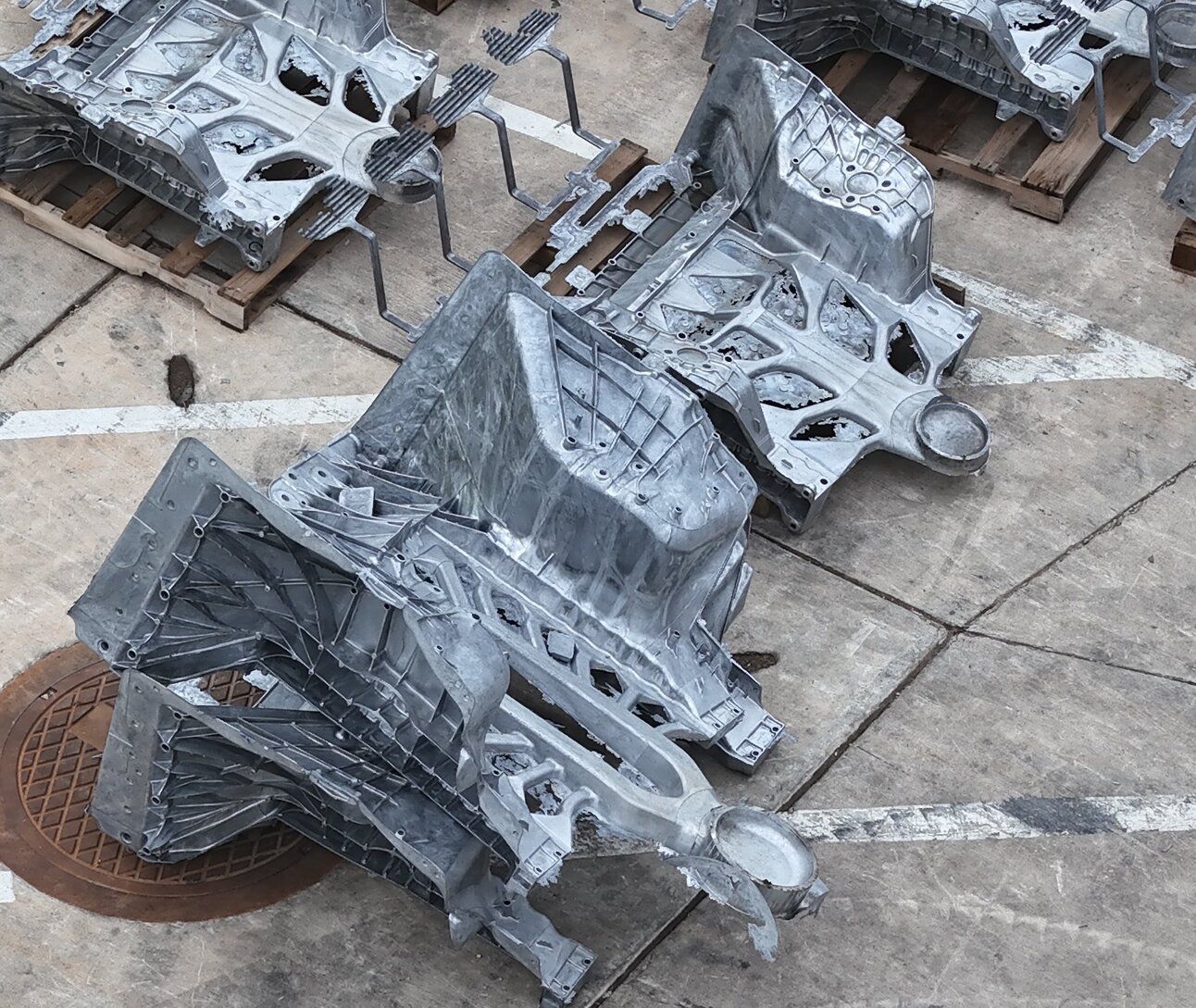
2 Cybertruck castings below, Cybercab above. Source: https://x.com/JoeTegtmeyer/status/1933534524459127288
❌ Don’t leave your insights to chance with social media algorithms
✅ Subscribe for free to receive updates delivered to your inbox
💡 Join thousands of industry professionals who rely on The Gigacasting Newsletter for the latest updates on Gigacasting, Thixomolding, Rheocasting, and more
📨 I’m dedicated to keeping your inbox clutter-free with updates sent every one to two weeks